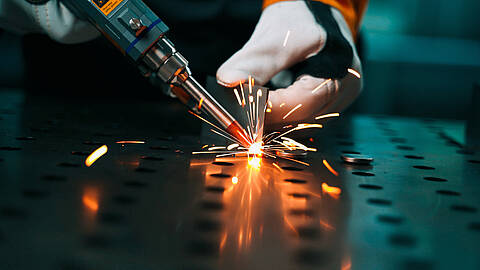
Burning for the perfect seam
Cobot welding robot and hand laser welding in focus
‘Welding is like sewing, only with fire. Anyone who has ever tried it knows that it is not easy. And it's more dangerous than sewing. It's not for nothing that there are countless training and further education courses on the subject of welding. But the welding industry is also complaining about a shortage of skilled workers. Companies are increasingly faced with the challenge of finding well-trained skilled personnel. How do you still get the perfect welds?
This was the question facing Jan Weiß, deputy branch manager of Blumenbecker Technik in Haiger. Among other things, the site specialises in the production of airport ground support equipment, such as so-called dollies. The answer has been in production in Haiger for about a year and is called ‘Cobot’.
Cobot welding robot - robots and employees complement each other perfectly
Weiß sought help from Michael Kerßenfischer, head of welding technology at the sister company Blumenbecker Industriebedarf GmbH. He recommended the collaborative robot, or Cobot for short. It consists of a robot arm equipped with force sensors. ‘The user simply pulls the Cobot by hand to where the welding is to take place. You don't need any previous knowledge of programming to set up the robot. But, you do need to know about the welding process, for example, to set the arc correctly,’ Kerßenfischer explains. The robot arm comes from Universal Robots (UR), the market leader for collaborative systems. The supplier for the complete cobot is Lorch Schweißtechnik, market leader for welding equipment.
In October 2022, the Blumenbecker site in Haiger received the Cobot for testing. After two days of training led by Kerßenfischer and his team, the Cobot was put to use for the first time; with success. ‘The device is easy to operate and the welding result is of consistently high quality,’ says Weiß happily. A small drop of bitterness: the system is limited to two free axes and pre-production errors are not compensated. Employees and Cobot have to work hand in hand; then they complement each other optimally.
No enclosure is needed for the Cobot. This lowers the costs. In addition, there is the time saving.Weiß and his team were convinced after the test phase. The system takes over the physical strain of welding caused by UV radiation, awkward posture and welding fumes for the employees.
‘Automating welding processes brings many advantages. The most obvious is the increase in productivity,’ Kerßenfischer knows. ‘We have already sold a few cobots and all customers were thrilled.’
Hand laser welding - for filigree seams without distortion
If narrow and filigree seams are required, Kerßenfischer usually recommends hand laser welding to customers. The energy source here is bundled light, which is applied by means of a ‘gun’. Less heat is generated in the welding process, he explains: ‘You can weld with welding wire or completely without. Then only the materials are joined.’ The advantage is obvious: hardly any distortion of the materials - no reworking, no cleaning, no straightening. And the
Training of the welder is sufficient. In addition, the safety technology must be observed for this procedure. You need a protective housing for the hand laser, suitable PPE and in any case a laser safety officer in the company. The result is perfect, high-strength welds of consistent quality. ‘Compared to the normal welding process, hand laser welding is much more energy-efficient, faster and more precise. It can be used where thin and filigree seams are needed.’
Competence centre in Beckum
Since 2023, interested parties and customers have been able to test hand laser welding at the in-house competence centre for welding technology in Beckum - under expert guidance, of course. Cobot welding and all common MIG/MAG and TIG processes can also be tried out here. ‘Testing new welding technologies yourself is often worth a thousand words. We analyse the requirements and recommend the optimally suitable products. We also carry out the training of the users,’ Kerßenfischer summarises.